Enhanced Inspections: One Year In
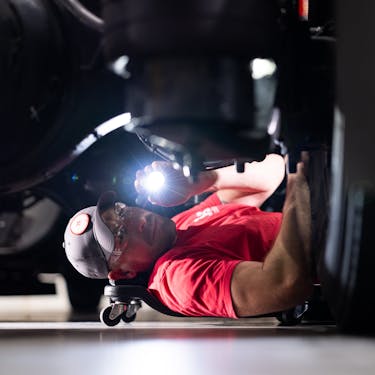
Autonomous trucks represent a unique opportunity to increase the safety of America’s freight ecosystem. Autonomous trucks never get distracted or drowsy, they don’t check their phones, and they’re programmed to comply with the rules of the road.
The potential benefits of autonomous trucks cannot be realized without a strong inspections regime that demonstrates to the public the roadworthiness of autonomous trucks. That being said, the traditional roadside inspection regime is a problematic fit for autonomous trucks. Most importantly, traditional Commercial Vehicle Safety Alliance (CVSA) North American Standard Level I Inspections require cooperation between drivers and enforcement during the inspection process - drivers are responsible for testing indicator lights, stepping on brake pedals, and otherwise demonstrating that key truck safety systems are operating properly. Conducting such an inspection without a driver in the cab raises significant challenges for fleets and law enforcement alike. Additionally, a core rationale for the roadside inspection regime is ensuring that drivers themselves are compliant with critical safety regulations, including Hours of Service.
In recognition of the unique enforcement needs of autonomous trucks, CVSA’s Enforcement and Industry Modernization Committee launched an effort starting in 2018 to create an alternate inspections program for Autonomous Trucks (AVs). After years of work in partnership with the American Trucking Association Technology and Maintenance Council, CVSA approved this framework, now known as the CVSA Enhanced Commercial Motor Vehicle Inspections (Enhanced Inspections) program at its September 2022 board meeting.
Enhanced Inspections require that a CVSA-certified inspector conduct a thorough inspection of an autonomous truck tractor and trailer combination, which is then valid for a 24-hour period. The Enhanced Inspection is a zero-defect inspection - should any single component of the tractor/trailer combination fail the inspection, the vehicle cannot be dispatched.
Once an autonomous truck is on the road, it must have the capacity to digitally communicate a Safety Data Message Set, which includes the outcome of the Enhanced Inspection as well as other relevant safety information, to roadside enforcement officers at inspection sites. This process ensures law enforcement has a high level of certainty about the roadworthiness of vehicles participating in the Enhanced Inspection program. While officers will of course retain the authority to pull over a truck should they have probable cause, vehicles participating in the Enhanced Inspection program will receive bypasses for routine inspections.
In April 2023, shortly after the approval of the CVSA Enhanced Inspections program, Kodiak, in concert with Drivewyze, a leading platform in connected truck services, and the Texas Department of Public Safety (DPS), launched a pilot of CVSA Enhanced Inspections along the I-45 Corridor between Dallas and Houston. As part of the pilot program, Kodiak inputs the results of each Enhanced Inspection into the Drivewyze system, which then wirelessly communicates the Safety Data Message Set to roadside enforcement officials in three inspection sites in Texas. This communication between the autonomous truck and enforcement officers, using the Drivewyze platform, is seamless to officers.
The success of the Enhanced Inspections pilot program demonstrates that Enhanced Inspections can solve a critical regulatory and safety hurdle to the commercial deployment of autonomous trucks. This significant experience can help guide regulators at the Federal Motor Carrier Safety Administration, state and local law enforcement, CVSA, and others as they look at potentially both expanding Enhanced Inspections, as well as adopting portions of the program for traditional trucks.
Pilot Findings
Since launching its Enhanced Inspections pilot in April 2023, Kodiak has performed Enhanced Inspections on over 1000 assets, including both autonomous tractors and traditional trailers. Over the course of these inspections, Kodiak has identified over 525 defects. Of those defects, 5% were found on tractors and 95% were found on trailers. The fact that trailers comprised the vast majority of defects is unsurprising. Kodiak already routinely inspected its own assets every day, and therefore has deep knowledge of the condition of those vehicles. On the other hand, Kodiak typically uses its customer trailers, so each new load Kodiak hauls typically comes on a trailer that has never previously received an Enhanced Inspection.
On the trailer side, 59% of Kodiak’s partners’ trailers passed their Enhanced Inspections. This finding likely reflects multiple factors. First, certified Enhanced Inspectors have a higher level of training and expertise than the typical driver conducting a Driver-Vehicle Inspection Report (DVIR) - they are therefore more likely to catch defects. More generally, trailers are often less well-maintained than tractors, both because trailers typically have longer replacement cycles than tractors, and because trailers often do not get serviced as frequently as tractors. Interestingly, 70% of trailers from these same partners passed a traditional DVIR, suggesting that the thorough nature of the Enhanced Inspections procedure can uncover additional safety defects beyond even a well-executed DVIR.
Because the Enhanced Inspection is a zero-defect inspection procedure, every defect identified during an Enhanced Inspection required repair before an asset could be dispatched. When Kodiak identifies a defect on a trailer, the company informs its partner that it will not be able to move the trailer until the defect has been corrected. Approximately 90% of the time, the partner will be able to quickly fix the issue before dispatch, but for trailers with multiple complex issues, they may choose to give Kodiak a new trailer that can pass the Enhanced Inspection.
While issues can be found anywhere throughout the inspection, the main issues are found in high-impact areas. During the course of the over 160 Enhanced Inspections of customer trailers that have occurred during Kodiak’s Enhanced Inspections pilot, Kodiak has identified 137 defects. 46% of those defects involved tires, including tread depth issues, sidewall condition issues, and flats. Another 10% involved broken or missing lights. Frame issues account for another 9%, while brake issues accounted for 4%.
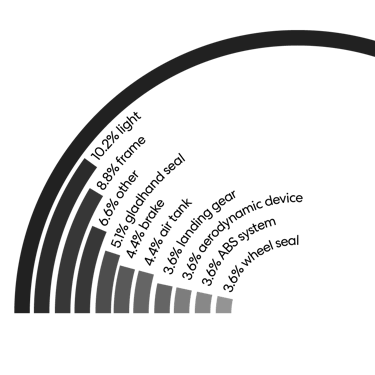
Enhanced Inspection Trailer Defects
Opportunities for Process Improvement
On average, Enhanced Inspections take 38 minutes to complete for a combination vehicle, or 32 minutes for a tractor only and 20 minutes for a trailer only. This is significantly more in depth than a typical daily driver pre-trip inspection, which, when performed properly, typically takes 15-20 minutes. Based on Kodiak’s experience, there are opportunities to streamline the inspections process without compromising safety. In addition, there is an opportunity to specifically enable the use of both AV self-diagnostic technologies and technologies like camera-based visual inspections and tire/alignment inspection devices. These technologies can not only speed the inspections process, but can help provide archived data that can further help improve safety. Additionally, as Enhanced Inspections become more prominent, it will be necessary to scale the training program to allow for a higher frequency of trainings and volume of inspectors.
Conclusions
The Enhanced Inspection program itself encourages fleets to achieve high maintenance standards. Given that every Kodiak tractor regularly receives an Enhanced Inspection, Kodiak has unique insight into its vehicles’ wear and tear. The Enhanced Inspections program therefore essentially becomes a robust proactive maintenance program that enables Kodiak to identify and correct issues before they become defects.
Kodiak’s data also suggests that Enhanced Inspections have the potential to raise safety standards across the industry. The in-depth trailer inspection required for Enhanced Inspections adds an additional safety benefit even after an autonomous trip. Indeed, several Kodiak partners have given the feedback that, rather than dislike Kodiak’s high trailer rejection rate, they appreciate the additional visibility Enhanced Inspections provide into their own trailer pools, and have used that visibility to improve their own trailer maintenance processes.
In conclusion, Kodiak’s first year piloting Enhanced Inspections suggests the program has the potential to raise safety standards while providing law enforcement, regulators, and the public with additional confidence regarding the roadworthiness of autonomous commercial motor vehicles. While there is more work to do both to refine Enhanced Inspection standard and expand it to additional jurisdictions, we believe the program represents a strong foundation for enforcement for autonomous trucks. Additionally, the quantity of defects found by Kodiak during the inspection process suggests that the certified pre-inspection model represents a genuine opportunity to raise safety standards across the trucking industry.