Huge progress. No shortcuts.
|
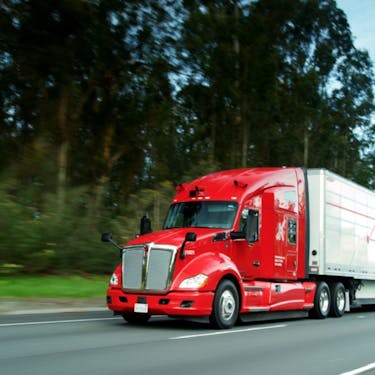
Kodiak looks back on a big year.
Going slow to move fast.
It was early December 2018, when Kodiak’s first fresh-off-the-line semi-truck rolled onto our lot. Our team got right to work. After preparing for months, we had three weeks to meet our ambitious aspiration of making our new truck drive a loop around our parking lot, without any human input to its throttle, brakes, or steering wheel.
Three weeks to get the truck ready for a spin. No problem, right? Well, when you’re talking about converting a truck into an autonomous vehicle, it’s actually a significant undertaking, with quite a few steps required to make it all work safely. The truth is that we had been preparing for this moment for months, building out our system, prepping all of the components, testing, testing, testing. Now it was time to put it all together.
First, we needed to install the cameras, lidars, radars, and inertial sensors. Then we needed to integrate everything with our main computer for communication and visualization and connect all of that to the engine, steering, and brakes. We had to add the in-house software that implements our artificial intelligence for autonomous driving. And we had to do it all while honoring our core cultural value: our commitment to safety. No matter how badly we wanted to see how our hardware and software would perform — and being engineers, we really wanted to get to work on our shiny new truck — we knew that shortcuts would create unacceptable risks, even in a parking lot at low speeds. We needed to know that we would be able to control the truck at all times, and that the brakes would function properly and predictably, no matter what.
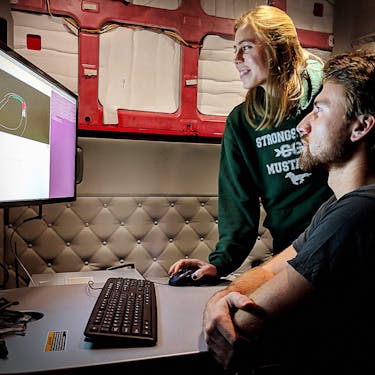
So we conducted the extended systems analysis that we had planned for months. We checked our experimental software in simulation over and over again. We verified the self-check system behavior that we had designed to prevent autonomous driving if any parts of the system were degraded. We set a precedent of testing and confirming safety overrides before every single autonomous drive.
We took the time to do it right, and because we had done our homework and put in the long hours before receiving the truck, we were able to hit our milestone of Kodiak’s first autonomous parking lot loop faster than we’d even hoped — in just two weeks and three days.
In other words, we were able to go fast, because we had gone slowly and carefully for a long time. All that work, all that willingness to put in the long hours on our upfront planning and testing, all of that commitment to executing methodically and safely, allowed us to take a huge leap forward without compromising any of our values.
That’s been our commitment from day one, and it’s not going to change.
In the year that has passed since that first test ride, we’ve added nine more semis to our fleet. Our team of software and hardware engineers, fabricators, technicians, technology professionals, and long-haul drivers has grown from 22 to 85 and counting. And we’ve ventured far beyond our Silicon Valley parking lot, validating our software in simulation and our platform in structured testing, putting our technology to the test in complex, real-world highway situations, and, yes, delivering commercial payloads. It’s been a year of progress without shortcuts, proving that we could go the distance while staying true to our values of safety and doing the right thing.
Kodiak’s first autonomous parking lot loop, December 2018.
Measure twice. Cut once.
We came into 2019 with a head of steam after that first test run in our parking lot, but the truth is that we could have purchased a used truck off of a lot on day one and taken a test run much sooner. Wouldn’t that have put us in a better position at the start of 2019? Why the wait?
Well, each used truck has its own distinct specs and countless variables. By definition a used truck would be different from our future fleet, and it would have come without documentation or other support. In other words, a quick demo run might have made good PR, but it wouldn’t have brought us any closer to a scalable, durable, and safe platform. It wouldn’t have taught us any lessons about how our technology actually works. It would have just been for show. We wanted to build our system on a solid foundation, so we’ve spent time developing partnerships with truck OEMs as well as sensor and actuator suppliers to build a platform that can be validated and manufactured.
Infrastructure is a funny thing: No one writes about roads and bridges that are flawlessly designed and impeccably maintained. But when a single element doesn’t work the way it’s supposed to, traffic backs up for miles — or worse, human lives are put at risk. The same is true for the system we’re building. For us, shortcutting our process in order to generate publicity was the moral equivalent of racing to complete a highway project without testing the concrete or working with a team of civil engineers. That’s just not how we do things.
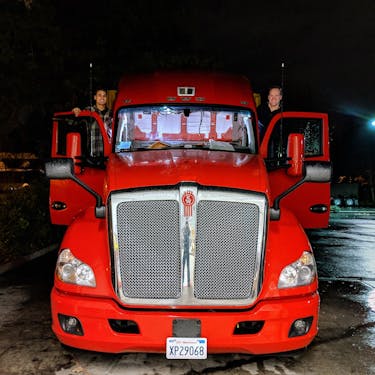
Early hardware installation on our first truck.
So, what does that mean in practice? For us, it meant focusing on our system architecture first, by building out a solid, reliable framework, to ensure that the first version of both the hardware and the software would allow us to test all of our system’s elements at the same time and provide a stable base on which to evolve our technology. We looked at every functional module in our system and asked how it would interface with everything else. We invested heavily in standing up our different modules and giving them the correct interfaces, even if their internal functions were still being developed, tested and refined. By asking hard questions early on, and building functional interfaces first, we set our team up to iterate quickly without disrupting upstream or downstream workflows. No workarounds. No reverse engineering.
The way we see it, there’s hoping for the best and knowing something will work. The stakes of autonomous trucking are simply too high for wishful thinking. So we wait until we know that we’re ready to take the next step. And when we do take a step forward, we know we won’t need to take it back. That’s where the experience of our team — led by industry veterans across the board — really makes a difference.
Getting real. On public highways with experienced safety drivers.
The lessons we learned from that first parking lot test run (and every run since then) directly informs the evolution of the system we’re building. A few weeks into 2019, our parking lot no longer satisfied our need for test runs. Closed-course testing, and the gradual addition of complex driving scenarios was our next step, with the goal of launching safe operations on public roads.
Autonomous trucking is new territory, with new and extremely important safety considerations. This is where the deep experience of our engineering and operations teams comes to the fore. As they built, tested and refined our system, our engineers asked questions like:
- How should we design and implement our maps, and how do we edit them?
- What’s the most robust way to fuse data from multiple sensors?
- What’s the most flexible and data-driven way to predict other vehicles’ behavior?
- How do we deal with ubiquitous uncertainty in perception and motion planning?
- How should we visualize the information our systems create and receive?
- How will we eventually determine that all components meet the bar to launch a product?
- How do we ensure operational safety at all times?
The list goes on and on. Taken on their own, many of these questions have short-term, relatively straight-forward answers, but missteps, especially with respect to how they interrelate, can have long-term potentially adverse consequences.
For example, maps are a critical component of all AV systems. As we built the foundation for a product that can scale, we realized current suppliers don’t deliver maps with the level of maintainability we require. So we built them ourselves, developing a system that can create accurate maps and update the entire fleet in near real-time when any changes to our route, like construction or infrastructure improvements, are detected.
Similarly, building a perception system based on tracked laser data seems like a good option initially, but it has a lot of issues with long-range objects and harsh weather conditions that are hard to fix later. That drove us to build our system using all sensors, and to heavily rely on cameras and radars.
We also went deep on the question of uncertainty — creating robust solutions to the challenge of unexpected behavior of other vehicles and unclassified objects on the road. The simple approach is to expect the perception system to mature and move towards being “perfect”; the experienced approach is to recognize that there is no such thing as a perfect deep neural net, and to characterize the expected imperfection. Uncertainty is possibly the single biggest challenge for the emerging AV industry, so we are tackling it head on from the beginning.
Finally, we built our system from the ground up with safety drivers in mind. As a result, they are encouraged to — and do — take control, seamlessly and with no surprises, whenever a potentially risky situation is on the horizon. We hire experienced safety drivers with stellar driving records, and from day one, ask them to disengage for the slightest performance issue or even when they feel the least bit uncomfortable rather than encouraging them to “let it ride” as a way of learning how our autonomy system will navigate tricky situations. We’ve chosen to capture information about these scenarios to model in stress-test simulations, rather than taking a less safety-first approach.
We took the same approach to every question our engineers brought up. We surrounded each technical challenge with a mountain of rigorously tested software engineering. We ran countless high-fidelity simulations, and we keep running them today as part of every change to our software.
Then, when we were ready and had completed an in-depth safety review, we began limited public road testing in autonomy with a safety driver in March. When we first engaged, we knew that it would work but had two hands on the wheel nonetheless. It was another big step that we were confidently ready to take.
Operating in Texas. Hauling freight for real customers.
The next few months were spent extending our area of operations in the San Francisco Bay Area, while implementing additional features such as truck-initiated lane changes. However, we knew that the place to grow our fleet and launch commercial services was Texas, so we began to build and train a team of Dallas/Fort Worth-based safety drivers, technicians, and operations team members.
When training was completed in July 2019, we sent our first truck to Texas. We mapped the critical highway stretches around our new offices, then moved on to test our code in simulation. Following that critical groundwork, we began driving autonomously on Texas highways. This might seem obvious to some — why would a truck not plug and play in another state — but for an autonomous system to work well in a different environment without a lot of adaptation or tedious mapping effort is hard work, and it again speaks to the quality and experience of our team and to the strength of the foundation we built before taking delivery of our first truck.
Kodiak trucks arrive in Texas, August 2019.
Texas has been a welcoming home for Kodiak. Not only have regulators and policymakers across the state been very supportive of our work, but its vast, freight-rich highway system also offers opportunities to operate in a wide range of traffic, weather, and road conditions. We focus on driving “hard miles”, in order to push the capabilities of our system and drive progress. Had we opted for easier miles — doing rinse and repeat runs on the same sparsely traveled roads, for example — we could have driven even more than the thousands of highway miles we’ve achieved in autonomy over the past six months. But we wouldn’t have learned as much, and we wouldn’t have continued to advance the long-term safety of our system.
The approach is paying off. We’ve recently begun running commercial loads for paying customers. This is giving us new insights into transfer hubs and other operational learnings all while helping us mature our technology. Our transfer hubs are strategically located, highway-adjacent lots that serve as exchange points for our freight. Skilled local drivers, who are familiar with area roads, bring commercial loads from distribution centers, and our safety drivers connect them to one of our autonomous trucks. The safety drivers then travel in the truck for the extended highway miles that make up the bulk of the trip. We call this the “middle mile,” and it’s at the heart of both our technology and business model. At the end of the “middle mile” journey, our trucks pull off the highway to another of our transfer hubs, where a local driver hooks up to the trailer and delivers it to its final destination.
Our transfer hub strategy allows us to leverage our autonomous technology on structured highways while human drivers focus on more complicated surface streets, leveraging their experience and expertise. Combined, this model increases operational efficiency at both ends.
From on-ramp to off-ramp. Reliably. Every day.
So, what’s next? We’re rolling into 2020 with all of our critical features tested. We’re ready to operate our trucks from on-ramp to off-ramp, using transfer hubs for the last few miles of each journey. We’re also able to drive autonomously on longer and more diverse highway environments. We will still use safety drivers, of course — and we will still disengage regularly to keep everyone safe on the road — but our on-ramp to off-ramp capabilities are making our system smarter and more resilient every day.
You might think we’d be focused on adding autonomous capabilities for surface streets to get from a shipper’s depot to the on-ramp, and from the off-ramp to another depot, but that’s not our priority. Our transfer hubs are a solid solution to that challenge for now, because while our team of industry veterans knows the ins and outs of street-driving AV technology, we also know that the hard part is not building the base functionality: it’s ensuring safe operation at all times. It takes many years to tackle all the challenging scenarios that are required in order to get critical safety verification and validation for surface streets done the right way. So instead, we’re making our highway system more robust, adding hardware and software redundancy, building a real product, and operating as a freight carrier for real customers.
From the very start, our goal has been to improve safety, enhance truck driver quality of life, increase efficiency, and reduce congestion and emissions. In 2020, we are going to continue improving our product reliability and efficiency. That means we’re getting closer to our product launch and we are working to make that a reality as soon as we can prove safe and reliable driverless operation.
We’ve asked and answered a lot of hard questions to get where we are today, but we know that this is just the beginning. In the coming year, we’ll be creating even more opportunities for problem solvers and innovators as we push ourselves to go the distance, without shortcuts.
If that sounds like the kind of journey you’d like to be on, let us know.
-Andreas Wendel, VP of Engineering
Interested in joining Kodiak? Drop us an email or visit kodiak.ai/careers
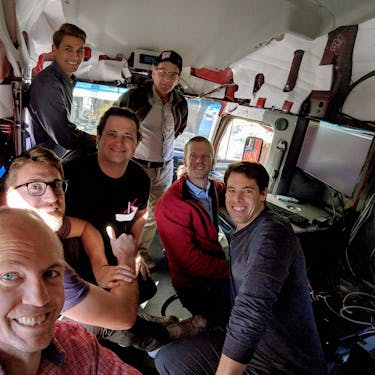